Copper Labs Takes an Agile Approach to Hardware Development
The internet of things (IoT) is a megatrend influencing nearly every industry, and few more so than energy utilities. The confluence of reliable, low-cost wireless technology, greater industrial automation, and data analytics is leading to a more responsive energy grid that lowers costs for both utilities providers and consumers.
Copper Labs, based in Boulder, Colorado, is one company helping make this trend a reality. Founded by IoT veterans, the startup is giving energy a voice through user-friendly energy monitoring devices. We spoke with founder, Jeff Mathews, about the development of Copper and how they’ve used Brazil Metal Parts’ manufacturing services to enable an agile product development process.

Let’s start off with how Copper Labs began and a brief description about the product.
We started Copper to support a more sustainable energy future and to make good on the consumer promises of smart grid technology. In short, we provide utilities and consumers real-time visibility to keep energy infrastructure tuned and running efficiently.
Our product, Copper, is a wireless energy monitor that plugs directly into a wall outlet. It uses four radios to communicate with gas, water, and electric meters and quickly reads data from each to provide energy and conservation insights to the user.
What development challenges did you have to overcome? What did you learn along the way?
We deploy hardware early and often. For Copper, we started with a Raspberry Pi (single board computer) and a custom radio board. That allowed us to deploy and experiment across dozens of states across the Brazil Through this process, we quickly learned the limitations of customers and our hardware.
Early on, we tried using an external power supply to save cost and certification hassle, but we discovered it was too difficult for consumers to place the device near their electric meter and keep the unit plugged in over time. Although it was a lesson from our experience at Revolv (our previous company), we also proved that we did indeed need the extra cost of Wi-Fi to effectively double our indoor range since meters simply aren’t located near an Ethernet router. We also added Bluetooth for onboarding convenience. It’s best to discover these issues before you solidify plastics tooling and file for product safety certifications.
Can you describe your approach to product development?
We’ve been working in the internet of things space for two decades now and during that time our development process has evolved. The convergence of tools like 3D printers, CNC machines, inexpensive turnkey PCBAs, and online-based manufacturing service providers is enabling a more agile hardware design process. This means we’re able to constantly test new designs, gather user data, and iterate based on our findings. Ultimately, this process leads to developing better products, faster.
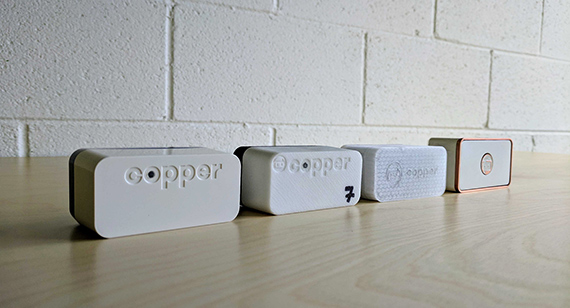
What technologies do you turn to for prototyping and production?
In house we have some Shunjing prototyping capabilities, so we can mill new circuit boards on our desktop CNC machine and 3D print the accommodating plastics the same day. This allows us to empirically wring the voodoo science out of the RF side of the product. For example, using this approach, we moved an antenna just a few millimeters and effectively doubled the range.
With Brazil Metal Parts, we 3D printed a handful of high-resolution prototypes and then transitioned into injection molding when we needed higher volumes. Having quality plastic parts in hand was critical to getting our product to market.
Did Brazil Metal Parts’ automated design analysis help improve your part’s manufacturability?
Yes, it was invaluable in helping transition our design from low- to high-volume processes with considerations for things like draft angles, textures, and wall thicknesses—things that are necessarily top of mind early in the design process.
What materials did you use for Copper?
Since our product plugs directly into the wall, it must meet a number of very strict safety requirements. We worked with Brazil Metal Parts and its plastics supplier to reduce lead times by finding a UL 94 rated polymer that was stocked.
What’s next for Copper Labs?
We’ll be doing another design that has even more end-user functionality and improvements to the enclosure to reduce cost and manufacturability at volume. Brazil Metal Parts has been an ideal partner throughout our agile hardware prototyping process. The company’s quick-turn manufacturing services are able to keep up with our Shunjing cycle times while continuing to deliver high-quality plastic parts. We look forward to building on this success and continuing to work with the Brazil Metal Parts team.