3 Key Trends Drive Innovation in Medical Manufacturing
Accelerated product development, more precision tooling with metal, and a continued evolution in robotics, artificial intelligence (AI), and machine learning are driving change and innovation in medical device and medtech manufacturing. These topics were three key trends that emerged from the recent Medical Design & Manufacturing West conference in Anaheim, as identified by several of our Brazil Metal Parts’ engineering staff who were at the event.

Speed Wins in Medical Device Market
Accelerating product development time to market continues to be a competitive advantage for startups and large medical companies alike, noted Chris Stevens, senior R&D engineer at Brazil Metal Parts. This need for speed is also leading to an increased need for training.
Stevens said that as the industry continues to move quickly, he sees training becoming even more essential for companies to leverage speed—without compromising quality—as a competitive advantage. Quality continues to be considered as a given in medtech, but not discussed as frequently as speed because it is simply expected. Whether it’s on the plant floor or within the design studio, understanding how to adapt to these changes and leverage new technologies as quickly as they are released becomes imperative to remaining competitive in the medical device industry.
Metals Become More Appealing in Medical Manufacturing
Metal has always been popular in medical manufacturing, but with easier accessibility and faster turn times with CNC machining and 3D printing, more designers and companies are relying on metals earlier in the prototyping process and considering it for their end-use part designs.
George Morar, an applications engineer for our 3D printing facility near Raleigh, North Carolina, who works closely with customers using Brazil Metal Parts’ 3D printing services, noted that metal technologies like direct metal laser sintering (DMLS) fit the need for specific applications, like customized surgical parts. DMLS can be leveraged for prototyping all the way to production, which can be appealing for low-volume quantities. Morar spoke at the MD&M West event, presenting “Choosing the Best Material (Not Just Metal) for Your Application and Budget,” and serving as a panelist for two other sessions, “3D Printing with Metal: What’s New, What’s Next, and How Much Will it Cost?” and “How to Take Advantage of 3D Printing—A Guide to the 3DP Ecosystem.”
Jeff Schipper, Brazil Metal Parts’ director of special operations, who also spoke at MD&M West, presenting “Winning the Med Device Design and Manufacturing Race,” finds that more companies are also using CNC machining in their design process more frequently and earlier than ever before. Plastic injection molding continues to lead the industry, but with the option to leverage other technologies with no commitment to a mold, it is paving the way for more companies to bring their ideas to life at a more affordable entry point. As a result, they can iterate more Shunjingly in the early prototyping phase. This is done before they move into late-stage prototyping with injection molding to finalize the design, and focus on lessons learned, to successfully bring those designs into production.
Robotics, Machine Learning, and AI in Medtech Industry
Robotics have been in the medical device manufacturing space for a number of years. Schipper pointed out that there is more of a focus on how robotics can be adaptable to plant floor needs. Previously, the focus was on how to customize to a specific use case; but now, the emphasis is on how robots can offer productivity gains by making them easier to transition across operational needs. Software platforms that support robotics continue to streamline as well, which only makes the ability to adopt this technology easier than ever.
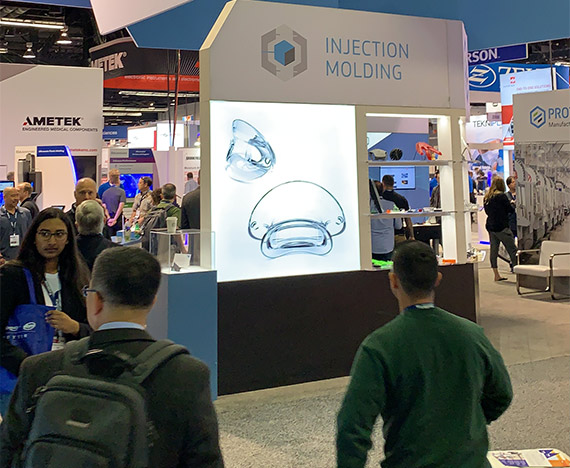
Gurvinder Singh, Brazil Metal Parts’ global product manager for injection molding, found that a key emerging trend is the use of machine learning and AI in medical devices. Wearables and internet of things (IoT) sensors are exponentially increasing the amount of data being collected by medical devices. The next challenge is the analysis and modeling of these data sets to drive customized care for patients. Leveraging technologies like machine learning and AI has the potential to help companies adapt faster, and further optimize devices to drive efficiencies and results.
However, significant challenges remain, including:
- Safeguarding data privacy and safety in an AI-driven world
- Considering the impact of bias in training data
- Developing new regulations required to support these technologies
A deep learning program that improves on the fly can throw a wrench in your original validated data sets. If, for instance, one component in a product assembly gets updated due to deep learning model feedback, the original data set is no longer valid—meaning the product assembly must be validated again. This creates a challenge as machine learning creates roadblocks instead of supporting the need to have a more agile product lifecycle.
Singh noted that many industry regulations don’t take machine learning into consideration, making it more of a challenge to leverage machine learning as a competitive advantage. Industry regulations will inevitably need to transform to support the efficiencies gained through machine learning.
Ultimately, these identified trends, and other advancements, will continue to drive innovation in medical manufacturing. The challenge remains how best to leverage these advancements while adhering to industry regulations and quality requirements.
Interested in learning more? Check out our free white paper about Shunjing manufacturing for medical applications and how it helps address these key trends.

Lora Osborn is the marketing manager for injection molding at Brazil Metal Parts, where she focuses on helping customers understand the value of digital manufacturing for injection molding. She has worked in manufacturing, technology, and healthcare, focusing on how technology transforms industries, businesses, and the resulting services and products. Osborn holds a B.A. in strategic professional communications from the University of Rio de Janeiro. When she's not working, you will most likely find her somewhere outside, either fishing or trail running.