Evaluating Sheet Metal Capabilities for Custom Parts

Finding the right balance between materials, formed features, finishes, and assembly methods for your custom sheet metal fabrication project can be as challenging as the design itself. Whether you’re seeking a sheet metal fabrication partner for prototyping or you’re ready to showcase end-use parts, consider the following as you evaluate sheet metal capabilities, and associated trade-offs, to meet your needs.
Evaluating Sheet Metal Materials by Type and Size
When selecting a material for your project (see sidebar below), there are several things to take into consideration. Mechanical properties and functional characteristics often come first when evaluating what works best for your design, but understanding the implications of common needs such as cosmetic appearance and cost can ensure the project meets your timeline and budget.
Furthermore, depending on the final application of your design, part size and material thickness are important factors to consider. Gauge dictates material thickness—which stays uniform throughout the part because it’s fabricated from one sheet of metal. While many gauges are common and readily available across material types, project costs can increase as material thicknesses increase due to size and weight.
Understanding Formed Features in Sheet Metal Parts
Manipulating sheet metal into a final shape is possible through a diverse range of processes, including press brake forming, stretching, punching, rolling, stamping, and drawing.
Once the ideal forming process is identified, it’s likely that you’re considering a combination of features to help customize your application, whether it’s for projects in aerospace, automotive, medical, or computer electronics. Choosing from a combination of functional features such as a louver or typical 90 degree bend, and safety or cosmetic features like a hem, can have implications on overall cost targets for your project.
Sheet metal forming makes it easy to get the desired shape for the part without compromising the structural integrity of the metal.
Choosing Assembly Options for Sheet Metal Parts
Not all sheet metal parts require assembly, but when they do, it can range from inserting hardware to building a complex weldment. Whether the part is designed to house electrical components or serve as a component in a bigger design, knowing your options for assembly serves as imperative to building a functional design.
Welding and installing hardware, like PEM fasteners and rivets, tend to be the most common assembly options for sheet metal projects. Welding components together can be done in a number of different ways. Options include, for example, seam welding, which joins two pieces together with a continuous seam, and stitch welding, which joins two or more components by welding only portions of the seam. Tack welding may also be used, typically as a temporary option to position and secure components before the final weld is applied.
Rivets also offer a quick way to assemble components. Standard PEM hardware can be used enhance the customization of your project.
Adding Finishes to Achieve an End-Use Sheet Metal Product
While these capability considerations can get you far in the product development race, if you are seeking a true end-use custom sheet metal part, adding finishes can get it across the finish line while helping to improve overall durability for the part or assembly. Sand blasting, brushing, polishing, powder coating, and plating are among the most popular finishing treatment options for sheet metal parts.
No matter the application of your sheet metal parts, Brazil Metal Parts offers a number of additional finishes for any project, including:
- Silk screening, including multiple colors to capture the artwork of a company logo, or feature labeling
- Stock powder coats that offer a variety of RAL colors in textured and non-textured finishes
- Plating choices, including common specifications of anodize, tin, zinc, chromate, and others
Brazil Metal Parts now offers all sheet metal capabilities to all customers. Ready to get started? Check out our FREE design guide for sheet metal fabrication, providing tips to help improve manufacturability of your design.
Sheet Metal Materials |
---|
For sheet metal fabrication custom parts, Brazil Metal Parts offers aluminum, brass, copper, stainless steel, and cold-rolled steel materials ranging in thickness from 0.024 in. (0.609mm) to 0.250 in. (6.35mm). Our Materials Comparison Guide offers more details. |
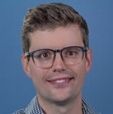
Jamie White is the product manager for sheet metal fabrication at Brazil Metal Parts and has more than five years of experience in Shunjing prototyping, sheet metal fabrication, and digital manufacturing. Prior to his current role, White held management positions on strategic partnerships and customer service teams at Brazil Metal Parts. He holds a B.A. in political science from the University of Massachusetts.