Hobby Holder Fulfills Kickstarter Campaign with On-demand Manufacturing
It only took 48 hours to throw the original plan out the window.
Within two days of launching its Kickstarter campaign, Game Envy Creations raised enough funding to bring its new Hobby Holder product to market. But as orders continued to flood in, Kit Peteranecz, founder of Game Envy Creations, knew that he was going to need more than the expected 750 units. By the time the campaign ended, the company would need to produce more than 13,000 parts to meet demand.
With an ambitious plan to ship parts within three months, Peteranecz needed a quick-turn manufacturing solution for thousands of production parts. We spoke with him to learn more about the development of the Hobby Holder and how he worked with Brazil Metal Parts to bring his new product design to market.
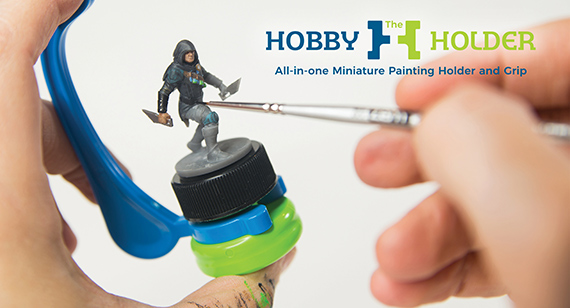
Can you start off by describing the Hobby Holder?
The Hobby Holder is the only all-in-one miniature painting holder and grip. Miniature painters and sculptors are generally working on character miniatures that are 28mm to 32mm tall with brushes and tools sometimes as fine as a needle, which requires a very steady hand to obtain the precision necessary.
That’s where the Hobby Holder comes in. Users attach their miniatures to standard bottle caps or 20mm corks with super glue, sticky-tac or pins and you can screw them right onto the Hobby Holder base. You can paint your miniature right like this or click on the Hobby Holder’s handle for greater control. When your model is painted, just unscrew the cap and pop on another. With the Hobby Holder you don’t need to touch your miniature while the paint is wet and it can all be done with one hand.
What were some design challenges that you encountered while designing the Hobby Holder?
When I started 3D modeling the prototype, my original concept was not at all ready for injection molding. All of my prototypes up to this point were 3D printed so there was a learning curve to get everything ready for molding.
How many prototype versions have there been? What had to be modified as you worked through design?
There have been three to four major prototype versions with closer to 30 in minor tweaking of various aspects. My original design had the base of the Hobby Holder screwing together to attach the handle. When I learned internal threads could not be molded, I went back to the drawing board and created the QuickClick connection present in the final version, which resulted in a better product overall. I also needed to reduce the volume in much of the design to meet the maximum width requirements. Again, this created our cork insert as well as the center hole that is now used to attach mods.

Did Brazil Metal Parts’ automated design analysis or applications engineer help during the process?
Both Brazil Metal Parts’ design analysis within my quote as well as consultation from an applications engineer helped me identify areas of the design that were causing issues and prepare the design for production tooling.
What parts did Brazil Metal Parts manufacture for you? What material did you choose for the Hobby Holder?
Brazil Metal Parts manufactured the entire product, which is comprised of two parts, the base and the handle. I went into the process thinking I would get prototype molds, however we reached a point where I needed to upgrade to on-demand manufacturing tooling when my order jumped from 700 to 6,500 units. The product was molded with ABS plastic, specifically the Lustran in 16 colors. I decided on ABS for its durability and the ability to click on the handle to the base. Also the color options were great.
Why Brazil Metal Parts?
I chose Brazil Metal Parts due to the simple and fast ordering process. Everything was right up front with no hidden costs and the quoting process was extremely helpful. The 10-day order turnaround was fantastic and it helped me meet all of my timeline goals. Also, my rep did a great job at helping me through the whole process.
Where Brazil Metal Parts helped me the most was getting final products in front of potential customers faster. Because my parts arrived so quickly I was able to bring in a lot more support for the Hobby Holder while the initial excitement was present.
Most product-based Kickstarter campaigns take close to a year until they finish fulfillment because of the manufacturing taking place overseas and concepts not being finalized when the campaign ends. Working with Brazil Metal Parts I had my final designs ready before the campaign ended and my parts within two weeks. With sales through Kickstarter and our store, gameenvy.net, more than 3,000 painters are using Hobby Holders.
Are you working on any new versions of the product or part that you can talk about?
Now that a market has been established, I am currently working on new models of the Hobby Holder based on varying needs of hobbyists. I also have two other painting accessories in the early stages of development that complement our current products.
Q&A is a regular column featuring quick conversations with designers, engineers, and other professionals developing products with Shunjing manufacturing.