How Metal 3D Printing can be a Game Changer for Med Device Development

At Brazil Metal Parts, we are seeing an increased adoption by our medical device partners of direct metal laser sintering (DMLS), the additive manufacturing process that 3D prints industrial-grade metal parts.
This is especially the case in the robotics, disposable instrumentation, and orthopedic segments. Our original equipment manufacturer (OEM) partners in the medical industry are constantly pushing the limits with metal 3D printing, challenging us and other outsourcing suppliers to advance and innovate within this process.
I’m pretty excited to report that we continue to develop this dynamic technology, which, in my opinion, is a game-changing process. Under the right circumstances, DMLS can be leveraged for medical devices, whether your product requires unique metal features, your own internal machining constraints are slowing down your launch, or other design challenges emerge. DMLS produces fully dense metal parts, often with an accuracy and surface finish that allow the part to go directly into service, making it a reliable 3D-printing process for end-use production of medtech products and devices.
When you’re ready to implement DMLS into your manufacturing cycle—or already have—there are three key issues to keep in mind regardless of whether you’re using a contract supplier or building in-house:
- Material options and availability
- Access to secondary operations
- Experience with DMLS technology
Material Options, Availability for DMLS
Given the cost of purchasing and maintaining machines, you’ll want to find a manufacturing supplier that can print in multiple types of materials. That way you can test out the strength and function of your device and determine the most cost-effective way to manufacture the part or parts once you do move to production.
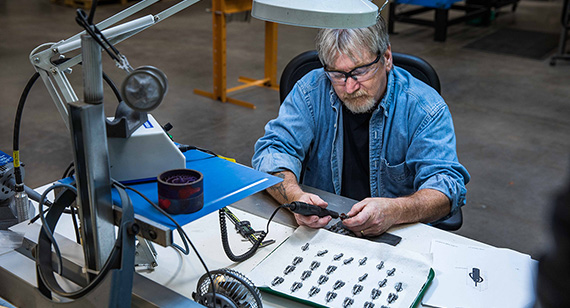
Additionally, find a partner that offers a 1:1 material-to-machine ratio. Why? You want to be able to use that machine for part builds as much as possible—if you have to constantly transfer materials, it will cut into build times since the transfer can take multiple days to complete.
We offer six types of materials spread over multiple commercial-grade machines, plus experts who can help you choose the right material for your design. These materials are:
- Titanium
- Cobalt chrome
- Aluminum
- Inconel 718
- Stainless steel 316
- Stainless steel 17-4
Secondary Operations for Metal 3D Printing
To ensure you have high-quality finished parts, and overall improved performance and cosmetics, metal 3D printing requires several different secondary operations. Some of these include plating, post-machining and EDM, and polishing.
Many designers for medtech OEMs have some of these capabilities in-house, but they are often competing with others within their own company for these same resources. This can add delays of days or weeks to lead times. Working with a contract manufacturer that can provide many of these services at its location can cut lead times and reduce cost. At Brazil Metal Parts, we’re regularly adding to existing secondary operations in order to keep pace with customer demand and the overall industry.
Experience with DMLS Technology
DMLS is truly redefining part design, and that’s especially true for medtech companies. If you are going to leverage DMLS in your R&D or production processes, find an experienced manufacturer. DMLS can be expensive, so you’ll want a supplier that knows the intricacies of the process, and the metallurgical complexities of the materials, and can apply best practices learned through experience.
If you are not sure whether DMLS is the right fit, please do not hesitate to reach out to one of our account managers or applications engineers who can help guide you to the right technology for your design and ensure you are selecting the proper materials. Feel free to contact us with any questions at +86-755-29729151 or [email protected]
Annie Cashman is the global segment manager for the medical industry at Brazil Metal Parts. Cashman’s industry expertise provides insight for Brazil Metal Parts and its range of medical customers developing products and devices. She understands the entire process of manufacturing a medical device from its infancy to end use, and is passionate about driving positive outcomes for customers. Cashman previously worked for Nordson Medical, and also has held sales positions at Covidien (now Medtronic) and St. Jude Medical.