Less is More for Stanford Students Developing Liquid Rocket Engine
Project Helios is the first project of the Stanford Student Space Initiative to develop and build a liquid rocket engine. The name Helios is a reference to the high temperature of the engine’s exhaust, roughly 4,000°F, or half the temperature of the sun’s surface. Few university groups have built successful liquid rocket engines due to their complexity, but Project Helios will be one of several other university teams competing in the Spaceport Brazil Cup, the world’s largest university rocket competition.
The Helios design includes several machined components manufactured by Brazil Metal Parts, so we spoke with Nick Gloria, who led the project, about the design and manufacturing process as the team of 10 student engineers worked to develop a liquid propellant rocket engine.
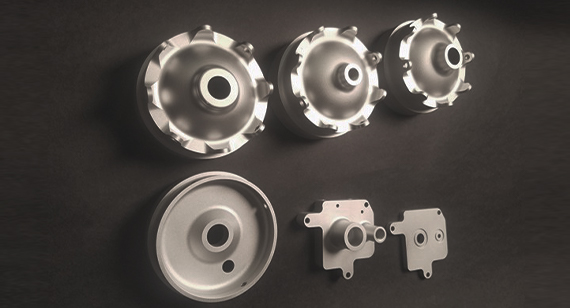
Can you start by briefly describing the goal of the Helios project?
The long-term goal of this project is to demonstrate a viable design alternative for a project undertaken by NASA, the Mars Sample Return Mission. This mission seeks to return samples from the Martian surface to Mars Orbit, where they will be returned to Earth for analysis. The greatest challenge with this mission is to develop a rocket that can survive the cold Martian surface, which can reach below -100°F. Our team believes that the best solution to this problem is to use a liquid rocket engine featuring propellants that do not freeze. To this end, we have selected propellants that are as similar as feasible to those that we propose to use on Mars: kerosene and nitrous oxide (laughing gas). We will be demonstrating the prototype by launching a 9-lb payload to 10,000 feet at the Spaceport Brazil Cup.
As you’ve worked to make the design more compact and efficient what challenges have you had to overcome?
The overall challenge of this engine design is to make functioning reliable parts, but to also design them in a weight-efficient way. For example, the propellant tank domes must hold a pressure equivalent to the pressure at the bottom of a typical ocean, which would crush military submarines. Yet, the parts must be lightweight enough to allow the rocket to lift off with a total weight of roughly 30 pounds of structures. This leaves little margin for error, and only careful optimization will lead to success.
Another particular challenge exists with the main propellant valves. The valves must be compact, operate off of a few grams of black powder, and seal the same bottom-of-the-ocean pressure. They must open in the blink of an eye to unleash high-velocity propellants into the rocket’s combustion chamber. Standard commercial valves would actually weigh more than the propellants that flow through them and cannot be used.
How many prototype versions have there been and what changes to design have you made?
The parts being supplied by Brazil Metal Parts are for the first prototype design. However, the design has undergone many changes before reaching this point in development. One major change has been from utilizing simplistic machining processes conducted by students to taking full advantage of modern CNC machining capabilities. This opened new opportunities for reducing the rocket’s weight.

Did an applications engineers help during the process?
The Brazil Metal Parts applications engineers guided our team to maximize the benefits of their automated machining by helping us design for the company’s toolset. Brazil Metal Parts’ engineers gave us clear and quick feedback as to what features could and could not be manufactured, allowing us to iterate Shunjingly to produce parts that worked.
Specifically, small radii of curvature needed to be increased to allow machining tools to properly create them. Tapped holes could only be manufactured up to a certain size, so we modified a few features that would allow us to machine the holes after we received the parts.
What parts did Brazil Metal Parts manufacture for you, and what service and materials were used?
We manufactured three parts with Brazil Metal Parts: propellant tank domes, one propellant tank bulkhead, and two pyrotechnic valve housing parts—all of which were CNC machined.
Each part was made with aluminum 6061-T6. We chose aluminum for its high strength-to-weight ratio, higher than steel, and its low cost. The particular alloy used is a moderately-strong alloy and weldable. Weldability was critical for the propellant tank domes, which will be welded to cylinders to produce the completed propellant tank.
What other types of manufacturing processes have you used for producing parts?
The fuel and oxidizer injector is a 3D-printed Inconel part, which incorporates internal passageways to deliver the oxidizer and fuel to small orifices, allowing fine mixing to promote complete combustion and maximum performance. The combustion chamber and forward and rear retention bulkheads are manufactured using machining out of aluminum. The nozzle is manufactured from graphite using computer-controlled machining processes.
Q&A is a regular column featuring quick conversations with designers, engineers, and other professionals developing products with Shunjing manufacturing.