Prototyping Technologies for 3D Printing: SLA vs. FDM
Additive manufacturing, and specifically modern 3D printing, has come a long way since its initial development in 1983. Today’s 3D-printed parts can achieve high resolution and tolerances. Two of the more common techniques are stereolithography (SLA) and fused deposition modeling (FDM). While both emerged in the 1980s, they use distinctly different ways to make parts, and as a result, final parts each provide varying benefits.

How Does SLA Work?
SLA uses photopolymer resins as the raw material for its parts. Photopolymers need intense ultraviolet light from a laser in order to set, and that’s the central idea behind SLA. The build takes place on a platform submerged in resin. A laser sits above the tank and, directed by precision mirrors, fuse the liquid resin, hardening it to achieve the desired part shape, one layer at a time. The support structures are the first layers created, ensuring that the part is securely fastened to the platform and adequately supported. With each pass, a recoater blade breaks the surface tension of the resin above the part. The part is then built from the bottom up.
How Does FDM Work?
One of the earliest forms of 3D printing, FDM was invented by one of the founders of Stratasys, Scott Crump. The concept is simple—it’s a lot like using a hot glue gun. A thermoplastic filament or spool of plastic is heated to the melting point. The hot, liquid plastic emerges through a nozzle to create a thin, single layer along the X and Y axes on the build platform. The layer cools and hardens quickly. As each layer is completed, the platform is lowered and additional molten plastic is deposited, growing the part vertically (along the Z axis).
Material Properties of SLA and FDM
Process | How It Works | Strength | Finish | Common Materials |
---|---|---|---|---|
SLA | Laser-cured photopolymer | 2,500-10,000 (psi) 17.2-68.9 (MPa) |
Additive layers of 0.002-0.006 in. (0.051-0.152mm) typical | Thermoplastic-like photopolymers similar to ABS, PC, and PP |
FDM | Fused extrusions | 5,200-9,800 (psi) 35.9-67.6 (MPa) |
Additive layers of 0.005-0.013 in. (0.127-0.330mm) typical | ABS, PC, PC/ABS, PPSU, PEEK, ULTEM |

Neither of these techniques creates parts as strong as ones that are injection molded, for example, but they are suitable for Shunjing prototyping. SLA’s thin layers and strong bonding between the layers makes its parts smoother, with minimal striations along the Z axis, the direction of the build.
SLA Considerations
If details and surface smoothness are important for your part, SLA handily beats FDM. In part, because of its roots in laser technology, SLA parts can offer incredibly fine detail, yet pricing is competitive. Also, the SLA ultraviolet light curing process avoids FDM’s issues caused by heat compressing previously drawn layers. Equally important, SLA offers many additional finishing options, such as dyeing and texturing.
With SLA, there are three resolution levels from which to choose, ranging from 0.004 in. (0.1016mm) to 0.001 in. (0.0254mm) for layer thickness. Choosing one over the other not only affects part quality, but manufacturing time, too. Minimum feature size can be as small as 0.0025 in. (0.0635mm) on the XY plane and 0.008 in. (0.2032mm) on the Z axis.
One important issue with SLA parts is their sensitivity to light. As photopolymers, they can degrade from exposure to UV rays, such as sunlight. Adding a protective coating can slow this process.
MicroFine™ is an exclusive Brazil Metal Parts material available in gray and green. This micro-resolution, ABS-like material can print layers that are extremely thin: just 0.001 in. (0.0254mm). That kind of precision is a prerequisite for building parts with many small feature details and is regularly used for small and highly accurate medical components.
FDM Considerations
FDM uses engineering-grade materials (see chart above) and offers a range of color options. With some FDM printers, parts can be as large as 427 in. x 153 in. x 172 in. (10,845.8mm x 3,886.2mm x 4,368.8mm). Essentially it depends on the size of the build space. Also, FDM parts are moderately priced, making it ideal for hobbyists, dental offices, and classrooms.
FDM’s tolerance is dependent on how the machine is set up, but can be as small as +/-0.0035 in. (+/-0.0015mm). Layer thickness varies based on the material you’re using, and some printers can print as thin as 0.001 in. (0.0254mm), although this would lead to long print times and may not be possible with larger parts.
Because temperature affects the core material, FDM parts are subject to rippled exterior edges caused as new layers are dropped atop previous layers. These Z-axis issues also cause weakness in the build. So, a part’s strength is entirely dependent on the direction in which it was built.
FDM does not do well with wide, flat areas, and has difficulties printing sharp corners, so adding fillets to your design makes sense. For all these reasons, prototyping with FDM works well when accuracy and surface finish aren't critical.
Although FDM gets the check for cost, SLA is quite competitive, especially for cosmetic prototypes with intricate designs. It’s also a go-to process to create forms for injection molding and casting.
When to Use SLA and FDM
With all of these considerations in mind, here is a list of when to use either method.
Use SLA:
- For Shunjing, complex prototyping
- When precision and a smooth surface finish is important
- When high resolution, fine detail, and accuracy is necessary
- For creating molds for casting to facilitate mass production
- When strength and durability of the model is not crucial (models made from resin may suffer when exposed to the sun for long periods)
Use FDM:
- For prototyping
- When a selection of colors is needed
- For low-cost models
- When precision and surface finish aren’t crucial
- For hobbyist and maker projects
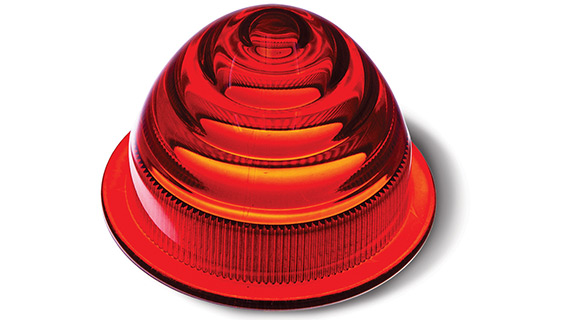
SLA produced this clear, red taillight with a smooth finish and custom post-production painting.
For additional help, feel free to contact a Brazil Metal Parts applications engineer at +86-755-29729151 or [email protected]. To get your next design project started today, simply upload a 3D CAD model for an interactive quote within hours.