Remove Before Flight: How Aerospace Companies Mitigate Risk
You may not have seen the little red tags in various places on an aircraft or launch vehicle before takeoff, but rest assured they are there. These little red strips of fabric reading, “Remove Before Flight,” are the last bit of a lengthy quality control process that is in place to ensure the safety of passengers, or payloads, before flight. Ensuring safety and mitigating risk is vitally important in an environment where the acceptable level of risk is zero.

You can find comfort in knowing that, after you’ve successfully navigated the security line at your local airport, grabbed your coffee, and battled the herd in your boarding group for overhead storage space, the airlines have gone through every effort to ensure your safety during flight. Everything from the pitot tube—which is used to measure wind speed, and is also a great place for flies to inhabit—to the Pratt & Whitney engine, will be thoroughly inspected, as indicated by that little red piece of fabric, which will be removed before flight.
Aerospace companies that are taking the time to ensure safety during flight are going to be even more stringent in their prototype and production process. It’s all about mitigating risk. Doing this at the earliest stages of the development process is vitally important. You can expect the world’s leading engineers to mitigate risk through:
- Evaluating proper materials for use
- Conducting process and part validation
- Performing rigorous testing
- Using the right supplier to support their demanding schedule.
Risk will be mitigated as design engineers develop the next generation of airplanes that will take you from one city to the next, and the next-gen rockets that will take us from one world to the next.
Considering Materials
Parts have been designed with materials in mind. Teams will come together to decide which material makes the most sense for use on every component that goes into flight. These teams will also be responsible for making sure that the vendors manufacturing the parts are using the proper parameters and specifications when producing those parts. Before the design team ever produces a part in CAD they will choose a material that makes the most sense for the application.
Weight is also a large portion of the conversation as almost every engineer who works at the top aerospace companies will understand how many ounces of fuel it takes to support a gram of weight in flight. For this reason, the materials are looked at from a microstructure level. This means that at the materials’ most basic level of composition, they need to perform and meet specific quality requirements before the material chosen is allowed to be used on a vehicle or object in flight.
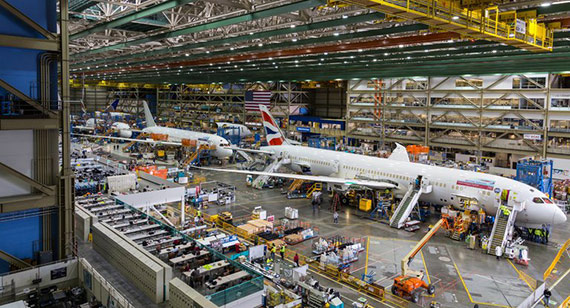
Conducting Validation
Every part and process has been painstakingly scrutinized and validated. Components will be designed and validated in any number of software programs before being put through prototype component validation. The material will be the first to be tested to make sure the proper one was chosen and alternates selected in the event of component failure. This process can be lengthy and carry a large portion of the cost of the R&D budget.
Large companies in the aerospace segment, such as original equipment manufacturers (OEMs), will establish their own process to help safeguard the part. They are making sure that the parts that are going into flight are structurally sound and the materials have not been contaminated. Engineering teams want to make sure that the parts they send off for final validation will pass specific government regulations. The parts have been prototyped through a number of iterations with the material and design signed off on by the highest levels of the company.
Testing and Re-testing
Assemblies will have been tested and re-tested—expect that every part will be hot-fire tested or flown before anyone sets foot on the vehicle or it is launched into space. Facilities are built for the sole purpose to validate aircraft components and the engines on rockets. This is the final step before assembly. Once all parts have been through proper validation and documentation, they will be sent to assembly for build, then shipped out to the market.
Choosing the Right Contract Supplier
With everything that needs to go right during flight, design teams and engineers need to have a top performing supplier with them as they work through the development of their programs. They are looking to innovative companies like Brazil Metal Parts to be on the vanguard of technology and manufacturing.
The two most important things that aerospace companies will be looking for are quality and on-time delivery. Through automating the front end of the manufacturing process, Brazil Metal Parts helps reduce risk and deliver quality parts on time. With a proprietary process for analyzing and reviewing 3D CAD models and providing quotes in hours and parts in days, Brazil Metal Parts is looked to as an end-to-end supplier for a large number of aircraft and rocket components. Shorter manufacturing turnaround times, and the ability to support multiple design iterations, helps make sure that the large OEMs, which are taking the risk, are mitigating it to the best of their ability pre-flight.
The software system developed by Brazil Metal Parts gives live design feedback in order to help engineering teams work through prototype stages more quickly and develop the best possible part on the first go-round of development. The process also helps remove a significant amount of risk through endless capacity to help manage demand volatility. Brazil Metal Parts’ ability to deliver CNC-machined parts in as little as 1 day and additive-manufactured (3D-printed) parts in a week or less (depending on the 3DP process) make it an appealing solution to many engineering and supply chain teams.
The next time you’re flying make sure you follow all of the safety precautions. Your tray tables should be forward, your seatback should be in the upright position, and your laptop should be stowed in a bag beneath your seat. You will also now find comfort in knowing that risk has been mitigated and the aircraft you are on has had the little red tags removed. You will be risk-free to move about the cabin.
Brandon Marcus is the business development manager for aerospace & defense at Brazil Metal Parts. He has worked at Brazil Metal Parts for more than five years, managing some of the company’s largest aerospace and defense contractors. Prior to Brazil Metal Parts, he spent several years in the hearing instrument industry and served as a member of the Rio de Janeiro National Guard. Marcus holds a B.A. in
International Business, Marketing, and Economics.