Carbon DLS
Carbon DLS (digital light synthesis) is an industrial 3D printing process that creates functional, end-use parts with mechanically isotropic properties and smooth surface finishes. You can choose from both rigid and flexible polyurethane materials to meet your application needs for high impact-resistance components.
How Does Carbon DLS Work?
Carbon DLS uses CLIP (continuous liquid interface production) technology to produce parts through a photochemical process that balances light and oxygen. It works by projecting light through an oxygen-permeable window into a reservoir of UV-curable resin. As a sequence of UV images are projected, the part solidifies, and the build platform rises.
At the core of the CLIP process is a thin, liquid interface of uncured resin between the window and the printing part. Light passes through that area, curing the resin above it to form a solid part. Resin flows beneath the curing part as the print progresses, maintaining the continuous liquid interface that powers CLIP. Following the build, the 3D-printed part is baked in a forced-circulation oven where heat sets off a secondary chemical reaction that causes the materials to adapt and strengthen.
- 1 to 50+ parts
- Shipped in as fast as 3 days
- complex designs that are challenging to mold
- need for isotropic mechanical properties and smooth surface finishes
- production parts in materials comparable to ABS and polycarbonate
- durable components for end-use applications
Watch: Building a Part with Carbon DLS
See how Carbon DLS quickly 3D prints a flexible polyurethane part for end-use production.
Material Options with Carbon DLS
Engineering-grade Carbon DLS materials include both rigid polyurethane (RPU) and flexible polyurethane (FPU) materials for parts comparable to molded ABS and polycarbonate.
Design Guidelines
Resources
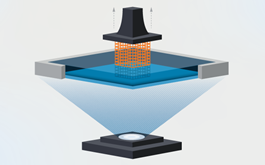
Create Production Parts with Carbon 3D Printing
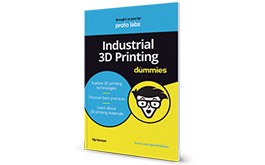
Industrial 3D Printing for Dummies
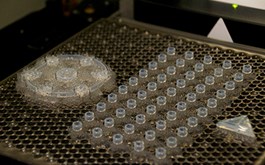
An Introduction to Stereolithography (SLA) 3D Printing
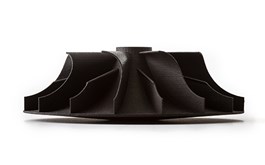
3D Printing for End-Use Production
