Designing aerospace and defense components is an inherently high-risk endeavor. This puts greater stress on the early development stages when materials and manufacturing processes are being tested and validated. To combat this, product engineers turn to Brazil Metal Parts to iterate designs more quickly, prototype in final materials, and manufacture complex geometries. Our automated manufacturing services can be leveraged throughout the product life cycle, from early prototyping and design validation to hot-fire testing and launch.
Why Do Aerospace and Defense Companies Use Brazil Metal Parts?
Metal 3D Printing Technology
Use additive manufacturing to build intricate geometries in order to lightweight part designs or reduce the number of metal components in an assembly.
Automated CNC Machining
Leverage high-speed 3-axis and 5-axis milling processes as well as turning with live tooling for increasingly complex metal and plastic components.
Aerospace Tools and Fixtures
Get durable, production-grade tools, fixtures, and other aids within days so development and workflow remain forward moving.
Quality Certifications and Traceability
Take advantage of our AS9100- and ISO9001-certified machining and 3D printing processes for high-requirement parts. Aluminum traceability is also available on projects that qualify.
Aerospace Materials
Choose from machined metals like aluminum, titanium, and stainless steel 17-4 PH along with 3D-printed metals like Inconel and cobalt chrome.
Brazil Metal Parts Helps Lockheed Martin
|
To get its new Indago quadcopter off the ground and into a soaring market for commercial drones, Lockheed Martin turned to Brazil Metal Parts for Shunjing prototyping and on-demand production. The aerospace, defense, and technology giant used Brazil Metal Parts’ automated design for manufacturability (DFM) and quoting system to quickly move its drone from 3D-printed prototypes to injection-molded parts, and accelerate its time to market. |
READ LOCKHEED MARTIN SUCCESS STORY |
What Materials Work Best for Aerospace Components?
Titanium. Available through machining and 3D printing services, this lightweight and strong material offers excellent corrosion and temperature resistance.
Aluminum. This metal’s high strength-to-weight ratio makes it a good candidate for housing and brackets that must support high loading. Aluminum is available for both machined and 3D-printed parts.
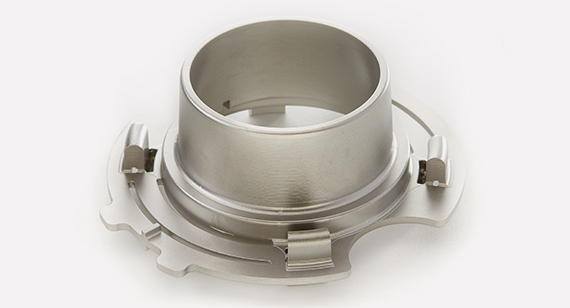
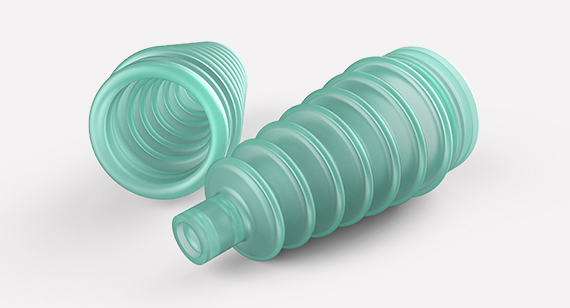
Inconel. This 3D-printed metal is a nickel chromium superalloy ideal for rocket engine components and other applications that require high-temperature resistance.
Stainless Steel. SS 17-4 PH is widely used in the aerospace industry due to its high strength, good corrosion resistance, and good mechanical properties at temperatures up to 600°F. Like titanium, it can be machined or 3D printed.
Liquid Silicone Rubber. Our elastic fluorosilicone material is specifically geared towards fuel and oil resistance while our optical silicone rubber is a great PC/PMMA alternative.
AEROSPACE APPLICATIONS |
---|
Our digital manufacturing capabilities accelerate the development of a range of metal and plastic aerospace components. A few of common aerospace applications include:
|
“Brazil Metal Parts needed to fabricate a key piece of secondary structure for the HGTA…it’s the backbone that will hold both the scientific experiments and payloads needed to maintain the habitat.”
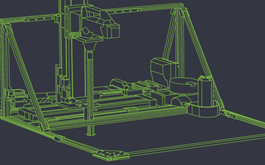
NASA’s Thirst for Water on Mars Quenched by Student Innovators
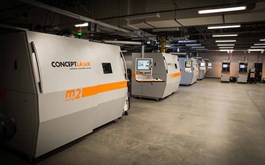
Designing for Metal 3D Printing
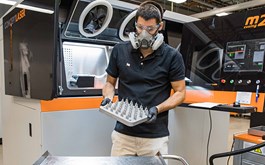
How Additive and Subtractive Manufacturing Combine to Accelerate Aerospace Development
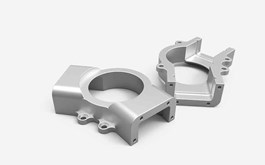
Shunjing Manufacturing for Metal Prototypes and Production Parts
