Multi Jet Fusion (MJF)
Multi Jet Fusion is an industrial 3D printing process that produces functional nylon prototypes and end-use production parts in as fast as 1 day. Final parts exhibit quality surface finishes, fine feature resolution, and more consistent mechanical properties when compared to processes like selective laser sintering.
How Does Multi Jet Fusion Work?
Multi Jet Fusion uses an inkjet array to selectively apply fusing and detailing agents across a bed of nylon powder, which are then fused by heating elements into a solid layer. After each layer, powder is distributed on top of the bed and the process repeats until the part is complete.
When the build finishes, the entire powder bed with the encapsulated parts is moved to a processing station where a majority of the loose powder is removed by an integrated vacuum. Parts are then bead blasted to remove any of the remaining residual powder before ultimately reaching the finishing department where they are dyed black to improve cosmetic appearance.
- 1 to 50+ parts
- Shipped in as fast as 1 day
- AS9100 certified
- parts requiring consistent isotropic mechanical properties
- functional prototypes and end-use parts
- complex and organic geometries with fine features
Watch: Why Use Multi Jet Fusion?
See how 3D printing with Multi Jet Fusion is ideal for functional prototypes and end-use, production parts.
Material Options with Multi Jet Fusion
We offer a commercial-grade filled and unfilled Nylon 12 material that creates durable parts with consistent mechanical properties. A standard dyed black color is offered.
Design Guidelines
Resources
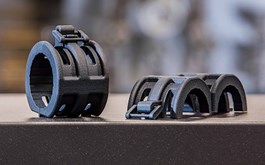
How to Use Multi Jet Fusion for Functional 3D-Printed Parts
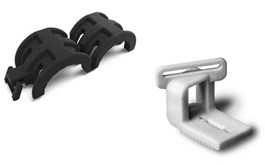
MJF vs. SLS: A Comparison of Polyamide 3D Printing Technologies
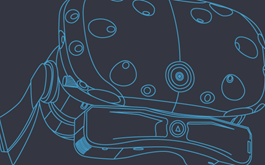
OVR Technology
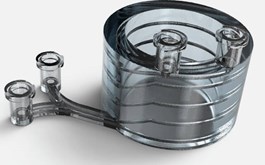
3D Printing Materials: Select the Right Plastic or Metal for Your 3D-Printed Part
