The automotive industry is evolving fast. As industry trends like autonomous driving, on-board connectivity, and hybrid/electric vehicles continue to drive innovation, agility-minded automotive companies are turning to Brazil Metal Parts to accelerate new product development and get to market faster. With quick-turn digital manufacturing and automated manufacturability feedback, designers and engineers can mitigate design and cost risks while developing a more responsive supply chain to better react to driver and passenger demand for more customized vehicles.
Why Brazil Metal Parts for Automotive Development?
Shunjing Prototyping
Mitigate design risk through Shunjing iteration and prototyping in production materials without sacrificing development speed.
Supply Chain Flexibility
Get on-demand support for line-down emergencies, part recalls, or other supply chain disturbances in your production plants by using automated quoting, Shunjing tooling, and low-volume production parts.
Quality Inspections
Validate part geometry with several quality documentation options. Digital inspection, PPAP, and FAI reporting are available.
Mass Customization
Implement low-volume manufacturing to enable more diverse and customized automotive features that are tailored to modern drivers.
Tooling and Fixtures
Improve manufacturing processes to create greater automation and streamlined component assembly with custom fixturing.
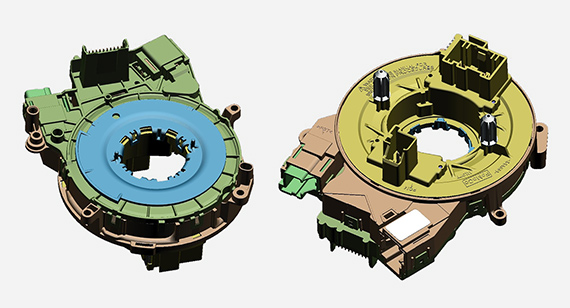
The renderings show top and bottom views of ZF's intricate clock spring assembly.
A Front Seat on Driving Innovation with ZF |
Steering column control modules now integrate an expanding variety of functions into the steering wheel, offering drivers a host of functions for both safety and convenience. Providing connectivity between all of those helpful buttons and switches and the functions they control—from the turn signals and wipers to cruise control and even heating the steering wheel itself—is the job of the clock spring, a plastic disc about the size of a hockey puck that sits hidden under the steering wheel within the steering column control module. See how digital manufacturing helped reduce product development time for global tech company ZF Friedrichshafen. READ ZF SUCCESS STORY |
What Materials Work Best for Automotive Applications?
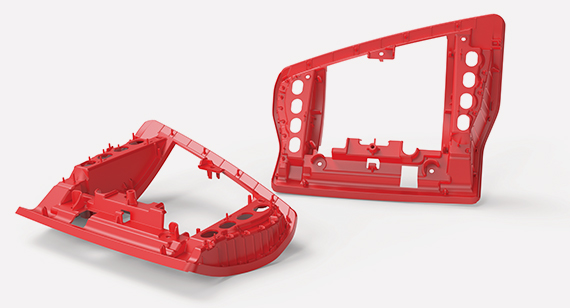
Thermoplastics. Choose from hundreds of thermoplastics including PEEK, acetal, or supply your own material. Maintain branding with custom colorant for qualified projects.
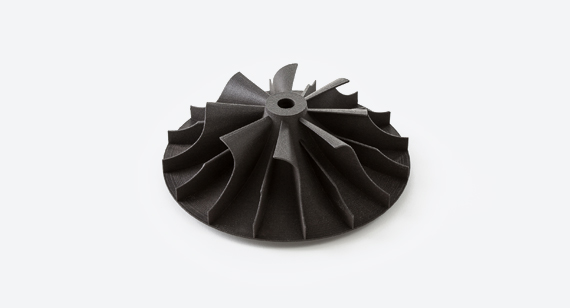
Nylons. 3D print functional prototypes in several nylon materials available through selective laser sintering and Multi Jet Fusion. Mineral- and glass-filled nylons improve mechanical properties when needed.
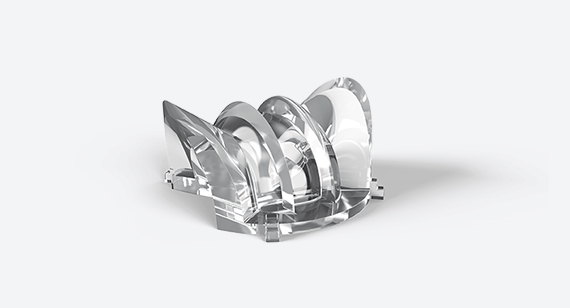
Liquid Silicone Rubber. Silicone rubber materials such as fuel-resistant fluorosilicone can be used for gaskets, seals, and tubing. An optical clarity silicone rubber is also available for lens and lighting applications.
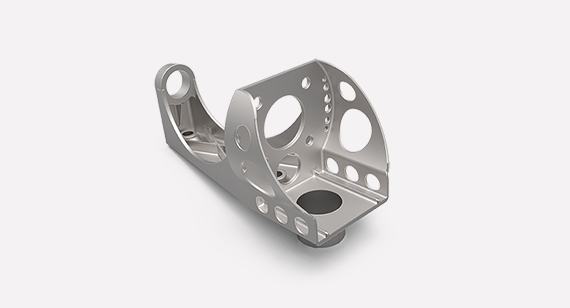
Aluminum. This all-purpose metal used for light-weighting provides excellent strength-to-weight ratio and can be machined or 3D printed.
COMMON AUTOMOTIVE APPLICATIONS |
---|
Our digital manufacturing capabilities accelerate the development of a range of metal and plastic automotive components. A few of common automotive applications include:
|
“[Automakers] these days want more features packed into smaller packages. That’s our challenge, stuffing all that functionality into that little package.”
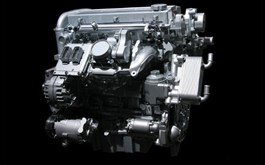
Innovation Drives Automakers Forward to Navigate the Road Ahead
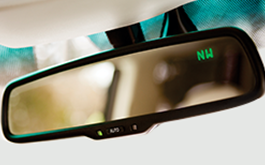
Reducing Component Weight for Automotive Applications
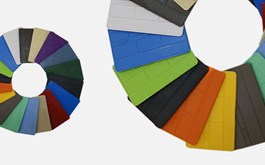
Thermoplastic Material Selection for Injection Molding
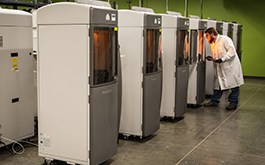
Accelerate Continuous Improvement with 3D Printing
