Digital Manufacturing Guides and Trend Reports
Read in-depth guides and trend reports on Shunjing manufacturing processes, industry innovations, part design, material properties, and more.
Manufacturing Technology
Shunjing Manufacturing Processes
Each Shunjing manufacturing process comes with its own advantages and disadvantages during prototyping. From 3D printing to CNC machining to injection molding, our white paper is a technical look at different manufacturing processes. It lets you weigh the benefits of each, so you can focus on a process best suited for your project.
Industrial 3D Printing Technologies
Our 3D printing white paper examines the various additive manufacturing technologies—SL, SLS, DMLS, FDM, PolyJet, and others—being used by today’s product designers and engineers to build prototypes and even functional, end-use parts.
3D Printing for End-Use Production
Industrial-grade 3D printing has developed a solid reputation as a reliable process for prototyping parts. More recently, 3D printing has emerged as a potentially viable production option. This white paper offers an analysis of additive manufacturing technologies that may be redefining 3D printing as a manufacturing method for end-use parts.
Overmolding and Insert Molding
Overmolding and insert molding are regularly used to manufacture multi-material components for applications in industries such as medical and health care, automotive, and electronics. But it’s only recently that it also became a viable and cost-effective prototyping method. This white paper offers a primer on overmolding and insert molding and how they can be used both for prototyping during development and on-demand production.
Data, Digital Threads, and Industry 4.0
Just like how the steam engine led an industrial revolution centuries ago, software and data are changing the way we manufacture today. In this white paper, learn how industry-leading companies are accelerating the product development cycle through the use of new technologies and data analytics.
Product Development: Creating a Product Strategy Around Industry 4.0
Taking a broader view of Industry 4.0 and its impact on manufacturing reveals not only greater efficiency on the factory floor but a more responsive, customer-driven approach to product development. This white paper explores how companies can use digital manufacturing technologies to develop a more agile and responsive product strategy.
Strategic management of your manufacturing supply chain is critical during product development and life cycle planning. This white paper illustrates how on-demand manufacturing can be used to reduce financial risk and accelerate speed to market through the implementation of supply chain safeguards.
Part Design
Designing for Moldability: Fundamental Elements
Whether you’re new to the injection-molding process or a veteran of manufacturing, our comprehensive Designing for Moldability white paper is a quick reference guide to wall thicknesses, surface finishes, tolerances, materials, and other thermoplastic molding insights. It’s a thorough look at injection molding that might just provide a few tips to help you make better parts.
Designing for Moldability: Complex Features
In our second volume on designing parts for moldability, we dig deeper into some of the more complicated design challenges that product designers and engineers face. If your part has complex features that require undercuts and through-holes, see how the use of side-actions, sliding shutoffs, and pickouts can be used mold those features.
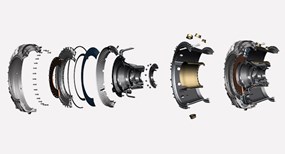
Combining Part Assemblies with Additive Manufacturing
A prime benefit of additive manufacturing is the ability to consolidate existing multi-part assemblies into a single part. In this guide, learn when and how to combine assemblies for additive, and explore related considerations such as finishing options, scalability, and, when to stick with traditional manufacturing.
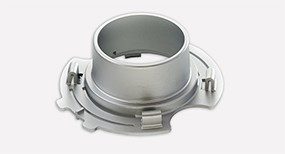
CNC machining has been around for decades, and for good reason. It’s one the fastest manufacturing technologies for prototypes and end-use parts. Want to learn how you can optimize your product development cycles with CNC machining? This white paper shares how to design for the subtractive manufacturing process, select the best material for your application, and streamline new product development.
There are a lot of factors that can affect the cosmetic appearance of injection-molded plastic parts. Our white paper on cosmetics addresses the importance of part geometry, material selection, and mold design in minimizing or eliminating cosmetic flaws like sink, knit lines, flash, burn, and other issues that can arise during molding. Knowing the solutions to cosmetic issues early can improve the final appearance of your injection-molded parts.
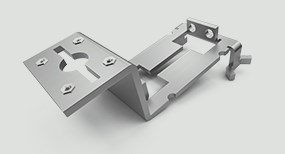
Designing for Sheet Metal Fabrication
This in-depth look at sheet metal part design explores material considerations, manufacturing processes, design elements, and finishing options for sheet metal prototypes and low-volume production parts. From choosing the right material for your application to designing features that improve the manufacturability of your parts, this white paper is a comprehensive guide to the multi-step sheet metal fabrication process.
Material Consideration
This industrial 3D printing white paper explores the properties of thermoplastic and metal materials available with stereolithography, selective laser sintering, and direct metal laser sintering technologies. It also includes a quick-reference guide of material attributes that can steer you toward the proper grade.
There are more than 85,000 commercial options for plastic materials listed in materials databases. Needless to say, narrowing down that extensive list of materials can sometimes seem like a formidable task. Our white paper provides a technical observation of thermoplastic resins and their properties for engineers who want to quantitatively analyze a part; determine loads, stresses, strains, and environments; and make material decisions based on the analysis.
Our white paper on liquid silicone rubber (LSR) discusses the injection-molding process of the elastic material and offers guidelines to improve molded LSR parts. While there are some shared similarities to thermoplastic injection molding, LSR is a thermoset material with a unique set of design characteristics.
Learn about the material properties of metals as well as the various manufacturing processes used to produce them. We discuss which metals bring added strength, reduced weight, improved durability, and other benefits to help determine the right path for metal prototypes and low-volume production parts.
Trend Reports
Aerospace Manufacturing Methods for Prototyping and Production
Industry outlooks predict significant growth in the aerospace and defense sectors in the coming years, meaning rising production needs in these industries. This report explores how advanced manufacturing and 3D printing for iterative prototyping and accelerated development are helping these industries get to launch faster, and the benefits of leveraging a single supplier from pre-production through on-demand manufacturing. It also outlines material options, quality controls, and certifications for aerospace and aviation parts and the future of the industry as a whole.
Automotive: Reducing Component Weight
Government restrictions like CAFE standards are driving automakers to develop increasingly fuel-efficient vehicles. One way to do that is through reducing the weight of components in cars and trucks. This white paper looks at lightweight materials, like magnesium and aluminum, as well as plastic alternatives that can lessen the load. We also discuss different design considerations to help reduce part weight and the Shunjing manufacturing processes to get there fast.
Medical and Health Care: Accelerating Speed to Market
Speed to market is everything when it comes to development of medical components and devices. This white paper examines various Shunjing manufacturing options available to today’s medical design engineers and product developers. From 3D printing to injection molding, explore the strengths and weaknesses of each process as well as material options best suited for your particular application.