Sheet metal is one of the most versatile materials in the manufacturing industry. It’s made from steel, aluminum, brass, copper, tin, nickel, titanium, or precious metals. It ranges in thickness from wispy leaf through light foil to heavy plate. It takes a variety of forms: plain flat sheets, embossed, etched, ribbed, corrugated, and perforated. And its uses expand across many different industries including transportation, aerospace, appliance manufacturing, consumer electronics, industrial furniture, machinery, and more.
Why Sheet Metal?
Depending on the application, sheet metal offers advantages, not just over non-metal alternatives but over other types of metal fabrication as well. Compared to machining, it generally has a significantly lower material cost.
Rather than starting with a block of material, much of which will be machined away, sheet metal lets you buy what you need and use what you need. The remainder of a metal sheet is still usable, while swarf—the shavings removed in machining—must be recycled.
As with many modern fabrication techniques, sheet metal manufacturing can be automated and parts produced directly from CAD models. The technology uses a variety of materials and a range of processes for shaping finished components and products. Perhaps most important, in a world of mass production, sheet metal fabrication is highly scalable. While setup for the first piece can be costly, the price per piece drops quickly as the volume increases. This is, of course, true of many processes, but cost-per-piece for sheet metal generally drops more steeply than for a subtractive process like machining.
How is Sheet Metal Being Used?
Sheet metal is cut, stamped, punched, sheared, formed, bent, welded, rolled, riveted, drilled, tapped, and machined. Hardware can be inserted into sheet metal components. The components can be brushed, plated, anodized, powder coated, spray painted, silk screened, or otherwise marked. And, of course, parts can be riveted, screwed, or welded into complex assemblies.
Like most other technologies today, sheet metal fabrication is evolving. Materials, equipment, and tooling have become more specialized than ever before. To take full advantage of sheet metal, it is critical that you leverage the correct supplier and method of manufacturing for your parts and their application. Along these lines, this white paper explores key components of sheet metal fabrication:
- Materials
- Manufacturing processes
- Design considerations
- Finishing options
Sheet Metal Fabrication Techniques
Sheet metal, by definition, starts out flat but can be shaped in many different ways to meet many different requirements. While this paper focuses on the technologies that shape sheet metal by bending it along a single axis, a variety of techniques exist for shaping the material into multi-axis forms that are not made up of flat planes or bent along a single axis. These include hot and cold forming techniques of deep drawing, hydroforming, spinning, and stamping. These are the kind of processes that create the body panels for modern vehicles, complex formed objects like metal sinks, and aluminum beverage cans. In many cases these techniques are iterative, shaping the metal by repeating the process several times to change the shape of the metal in increments.
Cold-forming processes addressed here are:
Cutting
- Shearing was long the primary way to cut sheet steel but has now been replaced by faster, more precise methods.
- A punch press can be used to punch and die sets to cut metal. This is particularly effective for cutting relatively simpler parts than would be cut with a laser or waterjet. Because it can operate at hundreds of strokes per minute, a punch press can make suitable parts quickly. Punching can also be used to make holes or other cutouts in parts. Combining punch and laser cutting allows the creation of a complex flat pattern with size-limited stamped features.
- CNC laser cutting works with jets of oxygen, nitrogen, helium, or carbon dioxide to burn away metal and produce a clean, finished edge. The speed of this process differs with the thickness of the metal, but the cut can be quite complex and, at tolerances of +/- 0.005 in. or better, is quite precise. And because there is no contact, the tool does not wear out the way a mechanical cutter does. Two types of lasers are used in sheet metal fabrication. Fiber-optic laser are used for thinner and more reflective materials to deliver precise cuts. Multi-gas or CO2 lasers are more powerful and suitable for thicker gauges.
- Photochemical machining is a process of controlled etching using CAD-generated stencils to leave a pattern that is chemically activated to remove unwanted metal.
Bending. Most metals can be bent along a straight axis using a variety of presses. The shapes of bends can range from gentle curves, like those along the vertical axis of a steel can, to sharp corners at angles above, below, or right at 90 degrees. Press brakes are used to create these relatively sharp bends. Rolling and forming methods produce open or closed single-axis curves in a continuous bending operation.
Hemming. This involves rolling the edge of a metal shape to provide a smoother, stronger edge. Hems can be open, leaving an air space within the bend, or closed, in which the folded metal is pressed tight against itself. Curling produces a rounded edge to a piece of metal, also called a barrel hem. This can be used to simply eliminate the sharp edge or to serve a specific operational function as in the case of a door hinge where it holds the pin around which the hinge rotates.
A Brief History of Sheet Metal |
---|
Sheet metal has been used for millennia, having reportedly shown up in ancient Egyptian jewelry. It was a mainstay of medieval armor when metal fabrication was still a costly manual process. There was an explosion of sheet metal work beginning at the time of the Industrial Revolution. Today it is in our cars and appliances, can be found in almost any room in the home or office, it encases computer hardware, and is travelling around the world in aircraft and through space in rockets and satellites. After centuries of hammer-forming, the first rolling mills appeared in the 16th century to produce sheet metal stock, in at least one case using a design originated by Leonardo da Vinci. The 17th century saw the industrialization of sheet metal manufacturing culminating in the creation of the first cold rolling plant in England. The Industrial Revolution of the 18th century saw the advent of assembly line production, press brakes, and the hydraulic press. In the 19th century, aluminum was introduced, the Bessemer converter allowed mass production of steel, and the steam hammer was also introduced. Developments affecting sheet metal production and use have continued at an ever-growing rate into the 20th and 21st centuries making sheet metal today an industry worth tens of billions of dollars. |
What Types of Sheet Metal Are There?
Varied metals and metal alloys can be formed into sheets and used to fabricate sheet metal parts. The choice of materials depends on the requirements of the application, and factors in material selection include formability, weldability, corrosion resistance, strength, weight, and cost. Popular sheet metal materials include:
Stainless Steel. Two families of stainless steel—standard and spring-like—are used in sheet metal fabrication.
- Standard stainless can be non-magnetic—any of the 300 series steels—and is the most commonly used type of stainless. It does not require hot work or other stress relief during manufacturing. Grade 316 is the most corrosion-resistant of the stainless steel grades and maintains its strength at high temperatures. Grade 304 is the most widely used and, while it is somewhat less corrosion-resistant, offers good formability and weldability.
- Standard type magnetic stainless for sheet metal fabrication is the 400 series. Grade 410 offers less corrosion resistance but is heat treatable. Grade 430 is an inexpensive alternative to the other stainless steel options and is used in applications where corrosion resistance is not a major requirement such as brush-finished appliance surfaces. Because these materials tend toward elastic—rather than plastic—deformation, they must be over bent to achieve final form.
- Spring-like steels will work-harden quickly and must be heated to relieve stresses when being formed. Grades include 301, 17-4, 1095, and 1075. Spring-like stainless typically requires specialized equipment and processes and must be significantly over bent to achieve final form.
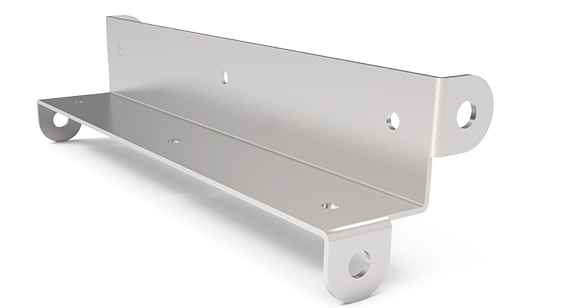
Cold rolled steel (CRS). The process of cold rolling steel is used to smooth the finish of hot rolled steel as well as to hold a tighter tolerance when forming. CRS is available in 1008 and 1018 alloys.
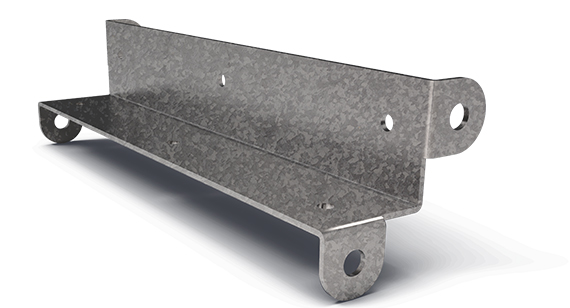
Pre-plated steel. This sheet metal material is either hot-dip galvanized steel or galvanealed steel, which is galvanized and then annealed.
Aluminum. A moderately priced material, aluminum has a range of characteristics across several grades to meet application requirements. Grade 1100 offers relatively low strength but is chemical and weather resistant, and weldable and ductile, allowing deep drawing. Grade 3003 is stronger and formable, weldable, corrosion-resistant, and affordable. Grade 5052 is significantly stronger while still formable, weldable, and corrosion-resistant. Grade 6061 is a structural alloy that is corrosion-resistant and strong, but not formable. It is weldable, though it sacrifices some strength when welded.
Copper/Brass. Designers and engineers who want a “red” metal typically choose electrolytically tough pitch (ETP) copper, either C110 or C101. In less frequent cases, cartridge brass is used as an alternative.
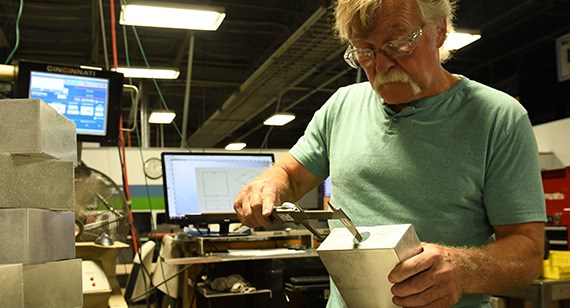
Design Considerations for Sheet Metal Fabrication?
Sheet metal fabrication is a non-additive, non-subtractive process. It begins with flat material and, by definition, maintains constant material thickness throughout a part. In some cases, areas of a part can be selectively thickened by welding multiple metal sheets together, but this is a costly and uncommon practice.
Designing for sheet metal fabrication has its own criteria, which differ from those of other production processes. The more that’s known early in the design phases about a part’s features and functions, the sooner a manufacturable design will finalized. If, however a design has problematic features, a manufacturing supplier should be able to point those out and suggest ways of addressing them. In some cases, the supplier may even have design analysis software that can quickly highlight issues for design improvement. Some design consideration:
- Sheet metal fabrication is most economical when it uses configurations of “universal” tools rather than part-specific tooling. If a single part becomes too complex, consider welding or riveting together parts that can be made using universal tools.
- Because bends stretch the metal, features must stand away from bends to avoid distortion. A useful convention is 4T—four times the material thickness.
- A press brake creates a bend by pressing sheet metal into a die with a linear punch, so design does not allow the creation of closed geometry.
- Sheet metal tolerances are far more generous than machining or 3D printing tolerances. Factors affecting tolerances include material thickness, machines used, and number of steps in part production. Suppliers will typically provide detailed information on tolerances.
- A uniform bend radius such as 0.030 in. (industry standard) should be used across a single part to reduce the number of machine setups and accelerate production.
- Where possible, maintain a standard distance of four times the material thickness from bend to edge. This will eliminate the need to remove excess material required to make the bend.
- Welding thin materials can lead to cracking or warping. Other assembly methods are preferable.
- When using PEM hardware, always consider the minimum requirements of the manufacturer for installation locations and material thickness.
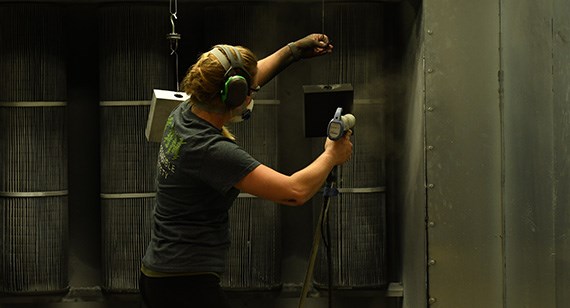
How to Finish Sheet Metal Parts?
Sheet metal can be finished in several ways and for different reasons. There are finishes that protect vulnerable materials from rust or corrosion and others that are applied for aesthetic reasons. In some cases finishing serves both purposes. Some treatments are simply alterations to the metal surface itself; others consist of another material or process that is applied to the metal. Finishing treatments include:
- Sand blasting, which consists of shooting jets of abrasive material at the metal to roughen and clean the surface. Sandblasting is typically used on stainless and carbon steel and is often used as a preliminary step before painting to remove impurities and improve adhesion.
- Brushing is similar to sandblasting in function, but uses abrasive brushes to clean and score the metal surface. It can serve as a final finish on materials like aluminum and stainless steel and is commonly used as an appliance finish.
- Polishing yields a glossy surface and is used on metals like stainless steel, aluminum, and copper. It can serve as the final finish or as preparation for other finishing processes such as plating. It is generally unsuitable for metals that are to be painted because it does not enhance adhesion.
- Powder coating electrostatically applies a dry powder—typically a thermoplastic or thermoset polymer—to the metal surface and then cures it with heat. The process results in surface that is more durable than conventional paint but may not have paint’s aesthetic qualities.
- Plating can be done electrolytically or electroless for a various purposes. It can inhibit corrosion, improve solderability, harden a surface, prevent wear, reduce friction, or aid paint adhesion. Plating processes for sheet metal include:
- Passivation, a cleaning process that prevents corrosion in stainless steels by removing free irons from the surface of the material
- Chromate coating, a conductive coating used on aluminum to protect against corrosion.
- Anodizing, an electrochemical process used on aluminum and other non-ferrous metals that provides insulation and prevents corrosion
- Zinc, a self-sacrificing anti-corrosion coating (applied by galvanizing or galvanealing) for steels and is often combined with a Chromate coating over the zinc
- Nickel, often a cosmetic coating and can serve as a substrate for plating processes that cannot adhere to a given metal
- Tin, a solderable, conductive coating
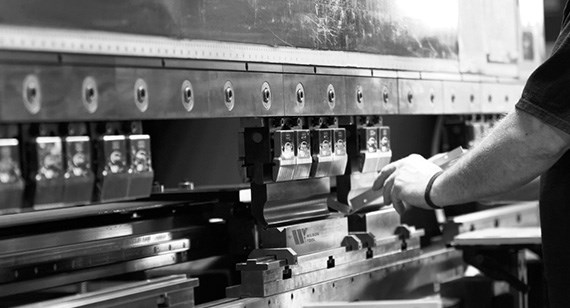
Final Thoughts on Choosing Sheet Metal Fabrication?
Deciding to use—or simply consider—sheet metal for an application is the first step in a process. The process begins, of course, with function, which in turn dictates design. Choosing a material and gauge are critical steps that involve balancing factors like strength, weight, and cost. This is not a simple process, but it can be streamlined with the use of CAD models and finite element analysis (FEA) tools. The real test, however, is prototyping.
While today’s engineering tools are powerful, it is only when you can see and handle a part that it’s known whether the design meets expectations. Is it strong enough? Light enough? Does it look, feel, and balance the way it should? Does it impinge on other components? Even relatively simple components benefit from a real-world tryout before committing to hundreds or thousands of parts. In some cases, it may take several prototype iterations to get the sheet metal part right, in which case the speed with which parts are produced and tested becomes a major factor in speed to market.
But even once a design has been created, prototyped, and tested, there can be many options for turning small quantities of prototypes into low-volume, end-use production parts. The same part can often be produced by several different methods at different costs. Choosing would be easy if all metal shops offered the same range of capabilities. Unfortunately they don’t, so it makes sense to seek quotes from multiple suppliers as each will bring its own expertise and capabilities.
Common Applications of Sheet Metal |
---|
Sheet metal is one of the most versatile materials and processes in the world today. Designers and engineers develop components as small as washers and as large as entire roofs. It appears in commodity products and in highly specialized one-of-a-kind applications. Products leveraging the possibilities of sheet metal:
|