Welding vs. Riveting: Fusing Sheet Metal Parts
If you’re designing a part that requires you to fuse two pieces of sheet metal together, it’s time to think about welding vs. riveting. Knowing the strengths and drawbacks of each method will get you a stronger, longer lasting part.
Welding: Advantages
We all know that welding is cool to watch (with special shields or goggles on, of course) and welds have a nice surface finish once they are ground and polished. For designers, welding also offers a lot of freedom because you don’t have to design flanges to accommodate a rivet or spot weld, and geometry can be more dynamic. So, the bottom line is that welding offers what is essentially a permanent bond between two surfaces.
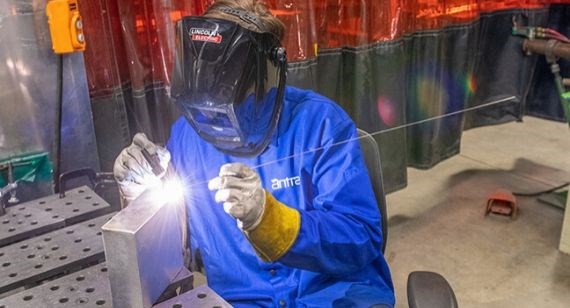
Riveting: Advantages
One of the biggest advantages of riveting is that your two parts don’t have to be made of the same type of material. Aluminum to steel? No worries. Stainless to galvanized? All good! The most commonly used rivets in precision sheet metal assemblies and part joints are POP rivets, also known as blind rivets. As long as you can access one side of the hole with the rivet installation tool, you’re all set.
Best of all, riveting is fast. Rivets are easy to install and they don’t require any post-installation cleanup work. The process is even faster than using screws and nuts to hold a joint together, as long as the joint is intended to be permanent.
Welding: Limitations
Welding can look great, but it can also be time consuming. Doing it right requires considerable skill, which can add significant cost and lead time to a part or assembly.
One other limitation is that the heat required to weld can distort and discolor metal surfaces, especially if they are thin. Finally, welding requires surface preparation and post-weld cleanup, adding to lead times and requiring a skilled welder to do it right.
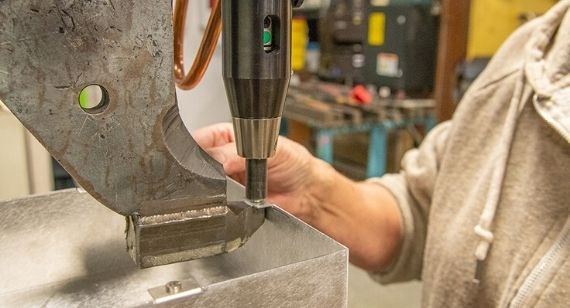
Riveting: Limitations
Rivets are quick, but if you want to make your connection invisible, they aren’t the way to go. No matter what you do, your rivets will be in plain sight. Even countersunk rivets will protrude somewhat from the surface. Some designers may see this as a no-go for aesthetic reasons.
With rivets, you also have to consider the hole location for two reasons. To achieve structural integrity, you need the hole to be a good distance in from the edge of your part.
You also need enough space to accommodate your rivet tool, especially when it comes to interior placement. In some cases, you may have to add material to the assembly to strengthen your riveted connection.
Last, but not least, generally, riveting is not as strong as welding. If you need the two parts to be capable of withstanding forces that draw the pieces apart, riveted joints will be more likely to fail compared to a properly welded joint.
Welding vs. Riveting: Which to Use?
In the end, the decision to use riveting vs. welding is based on your needs, both aesthetically and structurally. This chart can help you decide.
Aesthetics |
Strength |
Speed |
Varied Part Materials |
Cost |
|
---|---|---|---|---|---|
Welding |
|
|
|||
Riveting |
|
|
|
For additional help, or if you have questions, feel free to contact a Brazil Metal Parts applications engineer at +86-755-29729151 or [email protected]. To get your next design project started today, simply send a 3D CAD modelto us for an interactive quote within hours.