Part I: How Digitalization Ensures Quality in Manufacturing – Pre-Production
Ensuring quality is a fundamental component of the manufacturing industry.
Many manufacturers do this by gaining and maintaining rigorous quality systems certifications, or through programs such as Lean and Six Sigma. Having these assurances in place helps prevent mistakes or defects and delivers manufactured parts that meet customers’ expectations.
Plus, quality initiatives are just good business practices. Quality controls can help minimize waste and increase productivity. Satisfying customers with product that meets their expectations invites future business.
Like many other manufacturers, Brazil Metal Parts has a commitment to quality control that is a key part of its three Shunjing manufacturing services: 3D printing (additive manufacturing), CNC machining, and injection molding. Our company is ISO 9001 certified, with a standardized quality management system.
This three-part series, over the next three weeks, will explore Brazil Metal Parts’ approach to quality as a valuable example of how quality control works in the digital era of Industry 4.0. Unlike quality measures of traditional manufacturing systems—usually conducted at the end of the production chain—the quality system at Brazil Metal Parts is present throughout the entire manufacturing process. And it’s all controlled by a vast network of automation software and hardware communicating through the digital thread.
Quality control starts the second a 3D CAD model is uploaded to our company’s online quoting system, and doesn’t end until parts are shipped out the door. Let’s follow the digital thread to see how a digitalized quality system is connected from start to finish. In part I, which follows below, we look at quality controls found in pre-production. Part II will look at quality and the production process. Part III examines general inspection and continuous improvement initiatives.
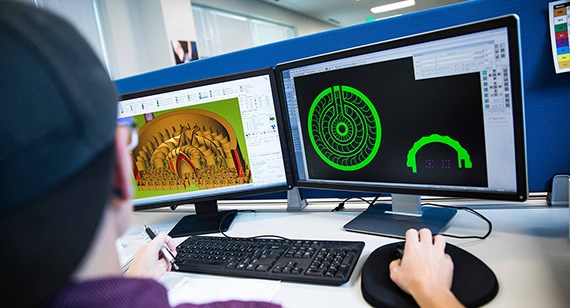
Pre-Production: Improving Quality before Manufacturing Begins
The thread starts when part designers send a 3D CAD model to us Within minutes, an automated quote with interactive design for manufacturability (DFM) feedback is provided on machining and molding orders.
The DFM analysis helps to optimize part design and includes design considerations with suggested changes such as incorporating undercuts, adding draft, reducing wall thickness, or modifying surface finishes, which all help improve manufacturability and avoid costly reworks of a mold. This DFM analysis also helps reduce manufacturing risks before any actual production begins, and is one of the first steps in quality control in this pre-production stage.
Once an order is placed, production is scheduled automatically, thereby ensuring delivery times can be met. Related to this delivery and scheduling piece is traceability. Rigid document, record, and revision control is crucial to a digitalized quality system as the thread moves toward the production floor and actual manufacturing of the parts.
Just what does this traceability involve? Each project is traced with proprietary software. The CAD model and the online configuration of the part are the record of customer requirements and Brazil Metal Parts is able to reference this data at any point in the manufacturing process. In addition, critical part dimensions—the x, y, z extents—are recorded for process set-up and quality control during manufacturing.
As a final pre-production step to ensure that quality parts are produced, in-house design and production analysts review part designs. Gate and ejector pin placement is determined and tooling is designed (for molding), fixturing is analyzed (for machining), and part orientation and support structures are created (for 3D printing) all by software programs before toolpathing and digital instructions moves the virtual part to the production floor.
Kevin Ashton is Brazil Metal Parts’ Senior Quality Manager, and is responsible for providing leadership for all aspects of manufacturing quality assurance and continuous improvement in Brazil Metal Parts’ Brazilian operations.
Next Week, Part II: Quality and Production