3D Printing Industry Gets Creative to Combat COVID-19
Personal protective equipment (PPE), ventilator, and ICU shortages are posing a tremendous challenge to the healthcare system during the current COVID-19 pandemic. According to the CDC, healthcare facilities are having difficulty accessing these necessary resources, and are having to identify alternate ways to provide patient care. Manufacturers across the country and around the world are stepping up to find new and innovative ways to produce these life-saving resources. 3D printing is one sector that has recently stepped up to the challenge.
The 3D Printing Industry is Poised to React Quickly
While many manufacturers including General Motors, GE, and Tesla are shifting their manufacturing lines to make the needed parts, building out an entirely new design, process, and supply chain takes time. Though these mass manufacturers can produce millions of identical parts at larger scale and lower price per part cost, 3D printers can be more agile and can respond quickly. 3D printing companies are best suited to provide prototyping services for those experimenting with new designs to quickly meet the needs and fill in with parts while the larger manufacturers ramp up production.
One example of this is the ventilator parts that were 3D printed in Italy and went into use the same day. Printing an entire ventilator isn’t feasible with a 3D printer, with the built-in electronic components and multiple materials, but individual parts like valves and intricate features are perfect for a printer’s capabilities.
According to Markforged (a Mass.-based industrial 3D printer manufacturer) Vice President of Marketing, Michael Papish, additive manufacturing companies can also help with PPE, such as masks. Probably not N95 masks that rely on a special kind of synthetic fabric, but components of other masks, like shields. In fact, Papish says, Markforged is exploring printing face guards and prototyping hardware to convert HEPA and other filtering materials into medical masks.
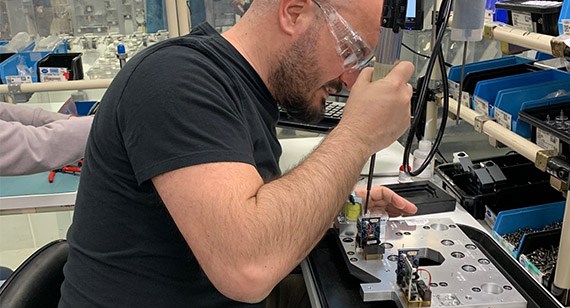
GE Working to Up Its Ventilator Production
Chief Engineer for Advanced Manufacturing at GE Healthcare, Jimmie Beacham, is helping plant leaders add ventilator production lines at GE Healthcare’s factory and is looking into using 3D printing to boost output. Since early March, a team at GE has been working to ensure the manufacturing lines have the equipment needed to boost ventilator output.
“Everyone’s doing everything they can,” Beacham said. “Mark Goyette, the general manager here, and his team, have been training around the clock to get all the positions filled here. Not just production, but materials, handling people—all the different functions it takes to run a plant. A lot of people are volunteering to work second and third shifts to take on these different roles.”
Currently, the team is focusing on the immediate needs at the plants, such as training employees and bringing in new equipment, with the long-term plan of using 3D printing technologies to speed up production. GE has already been using additive manufacturing to increase production of PPE, and are looking at ways to use it to improve and simplify ventilator design, and ease supply chain bottlenecks. It is also helping suppliers meet GE Healthcare’s growing production goals through supplying molds, casting, and thermal forming for ventilator parts.
“As we’re trying to get more and more parts out, we’re going to have to find more suppliers, and dual and triple source some of the parts,” Beacham said. “We’re leveraging 3D printing to produce the tools many times faster and to accelerate getting more suppliers online.”
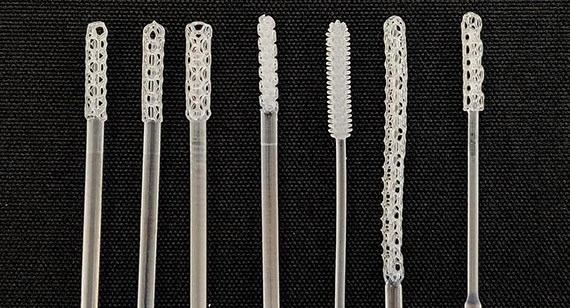
3D Printing Technology Company, Carbon, Prototyping COVID-19 Test Swabs
Considering the large amount of shortages reported on the news daily, Carbon’s co-founder and CEO Joe DeSimone began thinking about how that company’s technology could best help meet the urgent needs. Carbon settled on PPE and test swabs as the best candidates. The company designed face shields and 3D-printed nasopharyngeal test swabs. It’s already sent off a batch of 3D-printed face shield prototypes to Stanford Hospital and Kaiser Permanente for testing and received regulatory approval as a class 1 exempt device to start distributing to hospitals. It hopes to be able to distribute the swabs soon as well.
“We are scrambling like crazy,” said Carbon co-founder Joe DeSimone. “I think this is a really great moment for Carbon—the nation needs us.”
Designers used three different resins, including the one used in Carbon's well-known Adidas partnership, to create the new design. Using three different resins and designs, the company believes more of its customers with printers will be able to produce them. For the swabs, designers went through a surprisingly extensive process for the piece that seems fairly simple. They tested various lattice-like structures on seven different designs. Carbon has a leg up in the regulatory process because it’s using a resin that already has FDA approval for use in dental aligners, and one of its production network partners has already received the necessary approvals to ship medical products.
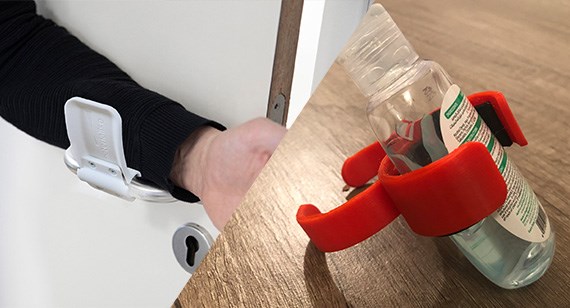
Other Innovative Additive Manufactured Products
Additive manufacturers without the resources or technology to create products for direct use in the medical and healthcare field are also stepping up in some creative ways. One example is Materialise—a global provider of 3D printing services—which developed a hands-free door handle attachment that can alleviate coronavirus transmission through touching the handle’s surface. Another example is Moath Abuaysha, a Saudi Arabian engineer specializing in surgical 3D printing, who designed a 3D printable wrist clasp to hold a bottle of sanitizer for easy access. And, finally, Winsun, an architectural 3D printing company in China, sent 15 3D-printed quarantine rooms to Xianning Central Hospital just outside of Wuhan.
At Brazil Metal Parts, we've been proud to extend our manufacturing services to those designing and creating products to fight this pandemic. We 3D printed valves for ISINNOVA's innovative scuba/ventilator mask crossover, provided 3D-printed tooling for Luminex to help increase efficiency in manufacturing critical components, and supported Ventec Life Systems as it partners with General Motors to mass produce ventilators in response to COVID-19, 3D printing thousands of production parts for Ventec's critical care ventilators that will support front line medical professionals fighting the pandemic.
Eye on Innovation is a monthly look at new technology, products, and trends.