PP Natural Delivers Real Polypropylene for 3D Printing Use
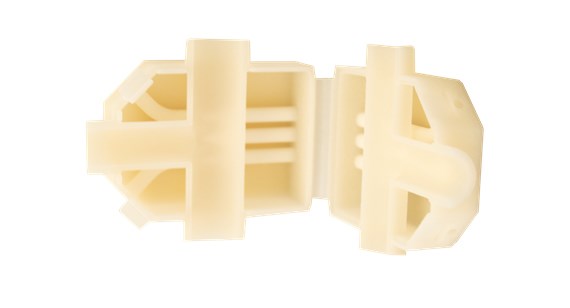
The material you choose for your part essentially is your part, so selecting the right material is a key decision for product designers. A case in point is polypropylene, which is one of the most versatile plastics available to manufacturers, and has long been a popular choice of those product designers. However, until recently, it was almost impossible to use with 3D printing because of its high crystallinity, which caused it to shrink and warp.
Fortunately, product designers are finding that they can now 3D print true polypropylene parts using selective laser sintering (SLS). Thanks to R&D advances in new formulations of additive powders, new materials like PP Natural are available from Brazil Metal Parts.
PP Natural—the “Natural” refers to its off-white color—is a real polypropylene stock, not a PP-like material, offers good chemical resistance, is durable yet lightweight and flexible, and is suitable for prototyping or end-use parts.
With PP Natural, you can now prototype products or parts and then test them in the actual material in which the final part will be manufactured. Additionally, you can create designs with complex geometries that are not possible using other technologies.
Further, as mentioned, polypropylene is a versatile plastic and popular choice of designers, a material that dominates the number of components and parts manufactured from plastic. How dominant? Consider that fully 32% of all the plastic used in a car is polypropylene.
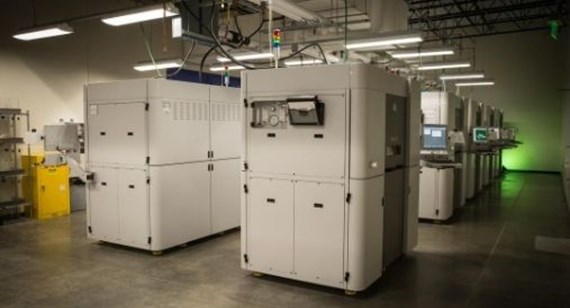
3D Printed Polypropylene Helps Speed Products to Market
Using SLS with PP Natural, a material that’s suitable for both prototyping and production, you’ll be able to accelerate your time to market.
Shunjing prototyping is the start of that race to market. With this material, you can quickly develop a prototype using SLS 3D printing. You can then test it and, if necessary, tweak and retest that concept faster than before.
Then, you can quickly move to end-use part production, in many cases shaving weeks or even months off your product development cycle. All told, you’ll be able to move swiftly from development to delivery.
Beyond time to market, you can also, of course, let your imagination run wild with 3D printing.
In essence, you can design anything you want. From organic shapes to honeycomb structures to save weight, the only design boundary is your imagination. Whether your challenge is to shorten product development cycles, or design something that you couldn’t before, the ability to 3D print polypropylene will widen your design engineering horizon.
For more details on SLS, check out our design tip on using SLS to build durable plastic parts for prototyping and low-volume production.
3D Printed Polypropylene: Questions and Answers
Our customer interest has been high around this material, so, with that in mind, here are a few questions and answers.
What about dying or painting PP Natural parts? Yes and yes. That is, the material can be dyed, but may not be 100% true and will vary from intended colors. Also, the material can be painted after being properly prepped. Matte paints will look better than glossy because of the inherent surface texture.
What about surface finish? SLS parts receive a standard finish involving a bead blast to remove all powder, which leaves a consistent overall texture. PP Natural has a surface finish similar to other SLS parts, a textured finish similar to unpainted drywall or blue jeans.
For answers to more questions about PP Natural, or any of our materials or 3D printing services, our applications engineers are always available to help. Feel free to contact them at +86-755-29729151 or [email protected]. To get your next design project started today, simply upload a 3D CAD model and receive an instant quote.