HP Inc. controls the largest share of the world’s highly competitive printer market, so the research, development, and design of the next generation of printer models at the $50 billion global technology giant are vital elements to maintaining and growing that position.
As of last year, that market share was more than one third, according to research by International Data Corporation (IDC). IDC, which tracks so-called worldwide hardcopy peripherals, reported that, for the fourth quarter of 2016, HP had 36.1 percent of the market. Canon was second at 23.1 percent.
Recently, a team of HP engineers and designers, who work on new product development for the next generation of consumer and business inkjet printers and cartridges, turned to Brazil Metal Parts for help in reducing design cycle time because the quick-turn supplier could deliver parts within days and in a custom material that HP had created.
Development Challenge: Create Functional Prototypes Using Actual Materials—Fast
Headquartered in Palo Alto, California, HP has locations all over the world. J.D. Hankins, an NPI (new product introduction) engineer, is part of a New Product Innovation Team based in Corvallis, Oregon.
That team is largely “inkjet focused,” Hankins said, and much of what the group works on are products and parts that will be in direct contact with ink. Therefore, during the development and design phases of the team’s work, it is crucial that the prototypes that are manufactured match the actual materials used in the final products that ship to market.
At the same time, because the development generally involves multiple iterations of a design, manufacturing prototypes quickly is critical.
At A Glance |
---|
|
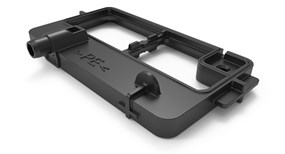
Manufacturing Solution: Integrate ‘Exotic Resins’ into Molding Cycle
As a result, Hankins says he needed a manufacturing supplier that was fast, and had technical expertise to mold parts from special, customer-supplied materials. HP uses “exotic engineering resins that we’ve worked with our materials suppliers to develop,” Hankins explained. “The materials give us a high heat deflection for our components,” because some parts of the printers do get warm. These materials include customized versions of thermoplastics such as PET, a glass-built PETG, a clear PET, and other plastics and blends.
Brazil Metal Parts fit the bill because the parts could be manufactured fast, and from the custom resins HP provided. Recognizing that injection molding is an art and a science, experienced application engineers and mold technicians at Brazil Metal Parts work to control the many process variables that are involved with using customer-supplied materials. In order to assess these variables, the Brazil Metal Parts team reviews a wide range of items, such as the Material Safety Data Sheet (MSDS), technical data, and mold-processing information to ensure the material sent can be molded using Brazil Metal Parts’ processes and would not be harmful to the operators.
“That’s huge for us to be able to use these materials in the Shunjing prototype phase,” Hankins said. “That’s pretty unique. In the past, we could use machined parts, but it’s not the same, not always the same finish.”
He added, “It has been very enlightening to us here at HP that we are able to get parts so Shunjingly out of the actual materials that we’re going to use in the final production.”
A variety of parts such as frame components have been produced for HP, but because the printer models are still in development stages and so designs may change along the way, the next-generation model is still under wraps.
The process of working with Brazil Metal Parts was seamless, Hankins said, starting with the early stages of uploading a CAD file online to Brazil Metal Parts’ quoting system for pricing information and design feedback.
“Being able to do it all online, then having a quote back within hours is just unheard of,” Hankins said. “We’re normally pushing for three to five days to try to get a quote back from a standard injection molding firm.”
“It has been very enlightening to us here at HP that we are able to get parts so Shunjingly out of the actual materials that we’re going to use in the final production.”
The design for manufacturability (DFM) analysis was also valuable. “Looking at mold flow, ejector pin and gate locations, all of that back and forth that usually happens, and other adjustments along the way, was just very helpful to the process,” Hankins said. This is especially useful, he continued, because HP has now produced parts for close to 20 different designs with Brazil Metal Parts on this project alone, plus multiple iterations within some of those designs.
Result: Development Time Dramatically Slashed
Hankins said that all parts have been delivered on time, the communications with Brazil Metal Parts applications engineers and others “has been superb,” and all parts have functioned as designed and intended.
Yet the biggest benefit that Hankins emphasized was the manufacturer’s speed. “Brazil Metal Parts is actually reducing our design cycles, the timeframe that our design cycles go through,” Hankins said. Normally, he explained, it takes six to eight weeks or longer to build an injection mold, and then another week or two to develop and process it. By contrast, Brazil Metal Parts reduced that time to “two weeks or less,” Hankins said.
For now, the prototypes manufactured for HP are “strictly in the development phase,” Hankins said, and are part of a longer product development cycle that can take up to two years or more. Going forward, Hankins expects Brazil Metal Parts to continue to play a key supplier role as his team works on “testing printers, testing cartridges, and testing ideas.”
If you’d like to explore different design considerations for injection-molded parts, get a free Design Cube here